A Lean Approach to Construction
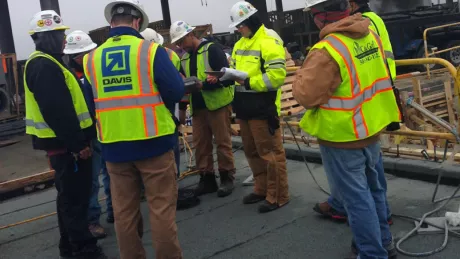
From the automotive to pharmaceutical industries, many companies apply lean methods, tools, and technology to their project management processes. Lean methods encourage transparency and communication between all project team members leading to maximized efficiency by reducing wasted time and unnecessary labor. The same processes are applicable and have become increasingly popular in design and construction project delivery. We’ve applied numerous lean principles to our projects that have enhanced our construction and delivery process, from start to finish, including one of our largest residential projects to date – BLVD at Reston Station.
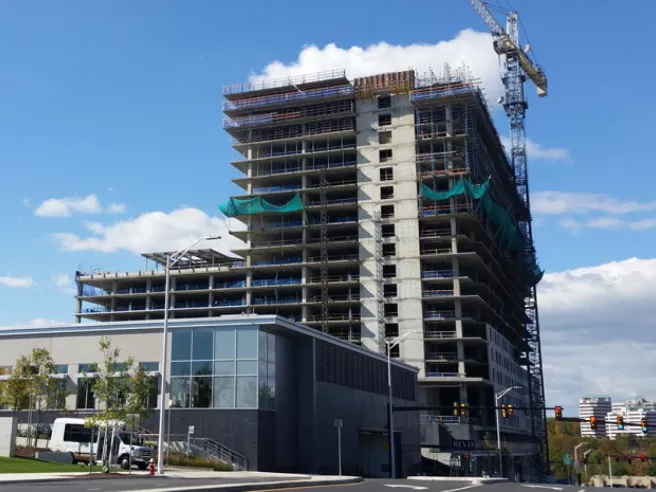
The Case for Collaboration
Upon completing the parking garage at Reston Station, the same project team moved on to start BLVD. In this next phase, the team wanted to adopt new processes and systems that would lead to more efficient work and allow them to capitalize on collaborative opportunities with subcontractors. First and foremost, they opened the lines of communication, creating an environment where information between team leaders and workers could be shared freely.
“Our trade partners are the eyes and ears on our project site every day. We want to know what they’re experiencing – good or bad. It’s important for them to know that we value their input.”
-Josh Majerowicz, Senior Superintendent, DAVIS
Daily meetings, or “huddles,” were held among project site leaders to build trust and establish a shared commitment to project success (pictured below). They were able to easily identify challenges, leading to shared solutions that were communicated to the entire project team. All of this helped avoid time delays and inefficiency as the project progressed.
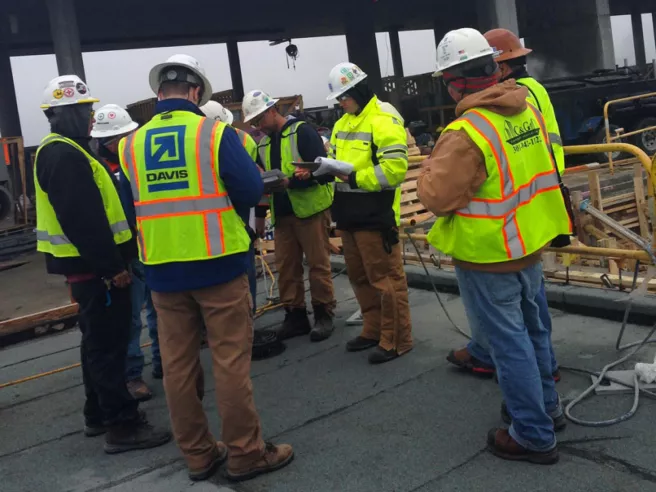
As part of our corporate quality management program, “first look” inspections took place throughout the life of the project. Instead of installing materials all at once, one item was installed and the process was reviewed to learn how best to conduct the work moving forward. To further improve the process the Last Planner System® (LPS) was introduced. LPS implements a series of scheduling and programming tactics, such as pull planning, to create and maintain buy-in at all levels at every stage in the construction process. Using pull planning to break down specific phases of the project as a group, the team was able to meet scheduling goals and client objectives together (pictured below). Throughout the process, the team was able to absorb significant structural design changes and still achieve the topping out milestone at 42 weeks as scheduled.
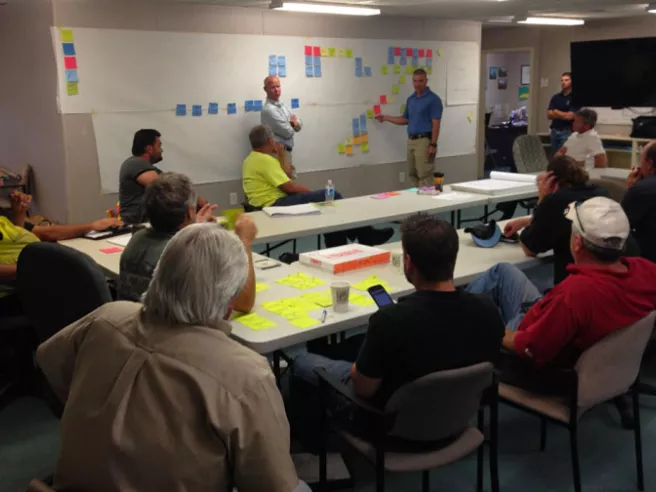
Expanding the Effort
BLVD at Reston Station was the first DAVIS project to be recognized for use of lean by AGC with a Washington Contractor Award. In fact, the project went so well that the team applied the same approach to their next project, a neighboring Office Tower at Reston Station. In 2017, nearly 40% of DAVIS projects currently incorporate lean principles – including some of our largest like 2000 L Street and 2U. We continue to adopt lean construction principles throughout all of our operations, even at the corporate level. Simply put, it’s a smarter, better way to build.
Recommended Reads
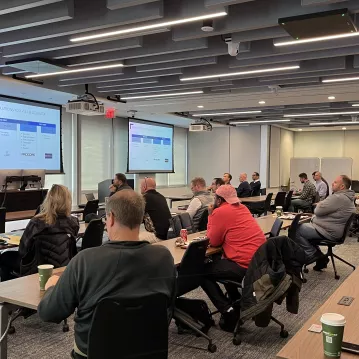
DAVIS Partnership Symposium
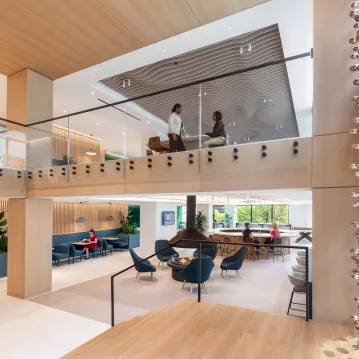
Q2 2024 | Market Report
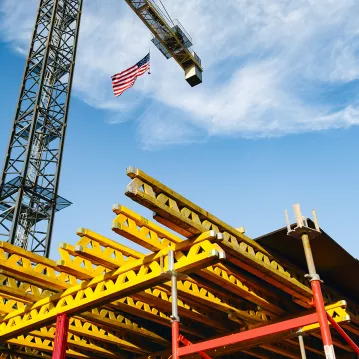